The smartphone aftermarket is booming like never before. Each company, be it a wholesaler, retailer, or recycler, chooses how to set up the workflow with devices; how to test, evaluate, and store them. Today, we will discuss the main methods, analyze the pros and cons, and calculate the efficiency.
There are three main workflow types: manual, software-assisted, and robotic. Manual testing is an unchanging classic where any company starts. As the business grows and develops, it becomes possible to integrate some technologies as a tool to increase productivity and streamline processes by minimizing routine tasks.
Manual Testing
The traditional approach. It relies on hands-on examination without special software or machines. Testers physically interact with the phones, checking functions like touch responsiveness, button operations, camera quality, and audio performance. Visual inspections identify external damages, such as scratches or cracks.
Cost assessment, for example, in trade-in programs, also occurs at the discretion of the store employee and may be biased, which leads to financial risks. If it's too expensive, the company loses money by overpaying; if it's too cheap, the client will leave unsatisfied with the price.
While manual testing offers a cost-effective solution for businesses with small volumes, it can be time-consuming and subjective, leading to inconsistencies in estimates. The method's accuracy largely depends on the tester's experience, making it popular among small retailers and wholesalers due to its minimum investment requirements.
Automated Testing
Larger companies gravitate towards software because it enables them to handle many items swiftly and precisely. The trend toward automatization among retailers and wholesalers is on the rise. With the aid of software, addressing these challenges has become more straightforward and expedited.
For context, the screen is its most susceptible component. A mere glance at the gadget can reveal chips, cracks, and other physical impairments. However, detecting issues like dead pixels or identifying non-genuine segments requires special programs.
Another point to consider is the absence of a standardized grading system. Technicians evaluate the cosmetic condition based on their personal judgment and experience. In contrast, the software employs a consistent framework across all platforms and gadgets, ensuring uniform grading outcomes.
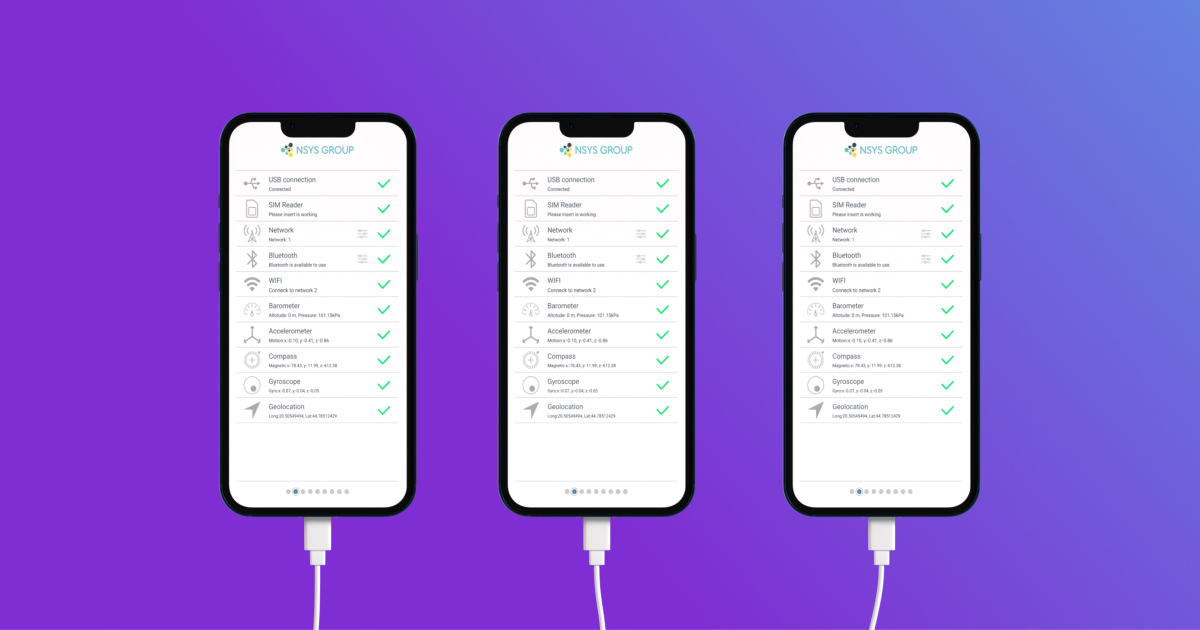
Robotic Testing
But what if there is an alternative that is even more compelling than software? Machine diagnostics is the most modern and high-quality processing option since it creates perfect conditions for checking visual status and audible signals.
Speaking of performance, the robot is extremely efficient. Let's look at the example of Reeva robor from NSYS. One technician with a robo-line can process up to 1,000 phones per day! Impressive numbers, right?
Diagnostic and grading accuracy is 100%! This was achieved thanks to innovative technologies and ideal conditions inside the machine. None of the most experienced staff members can check such numbers, even when working non-stop.
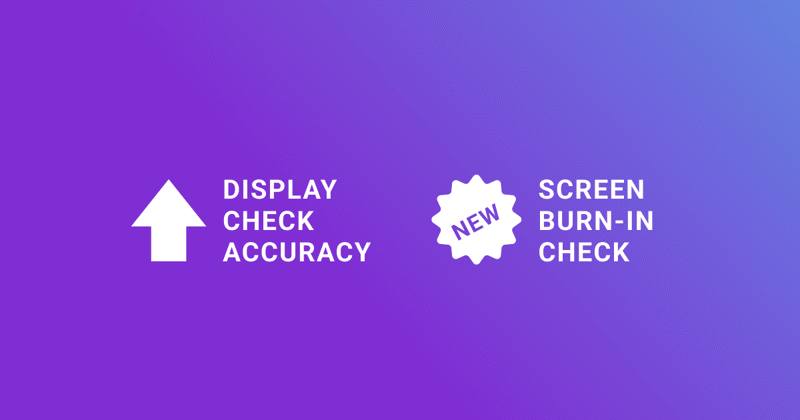
Training staff to operate the system is easy, making it ideal for companies with frequent personnel changes. Automation not only accelerates tasks but also facilitates round-the-clock operations, delivering more value for less expenditure.
Robotics also enables the generation of detailed reports on suppliers with a high incidence of faulty handsets, post-diagnostic reports, data deletion confirmations, and much more. The insights generated can guide your team in making informed future decisions.
Reeva Mobile Testing
We're perpetually exploring innovative methods to expedite and simplify functional testing. This led to the creation of Reeva, a groundbreaking solution that promises cost-efficiency for both retailers and wholesalers.
Reeva oversees the entire diagnostic process. While it retains all the benefits of software, its capabilities have been elevated. Tests such as evaluating the external condition, inspecting the display, load testing, or audio testing quality are more precise.
Images are captured under uniform requirements, and the speaker tests are devoid of any irrelevant noise. A notable addition is the screen burn-in check. This takes quality assessment to unprecedented heights.
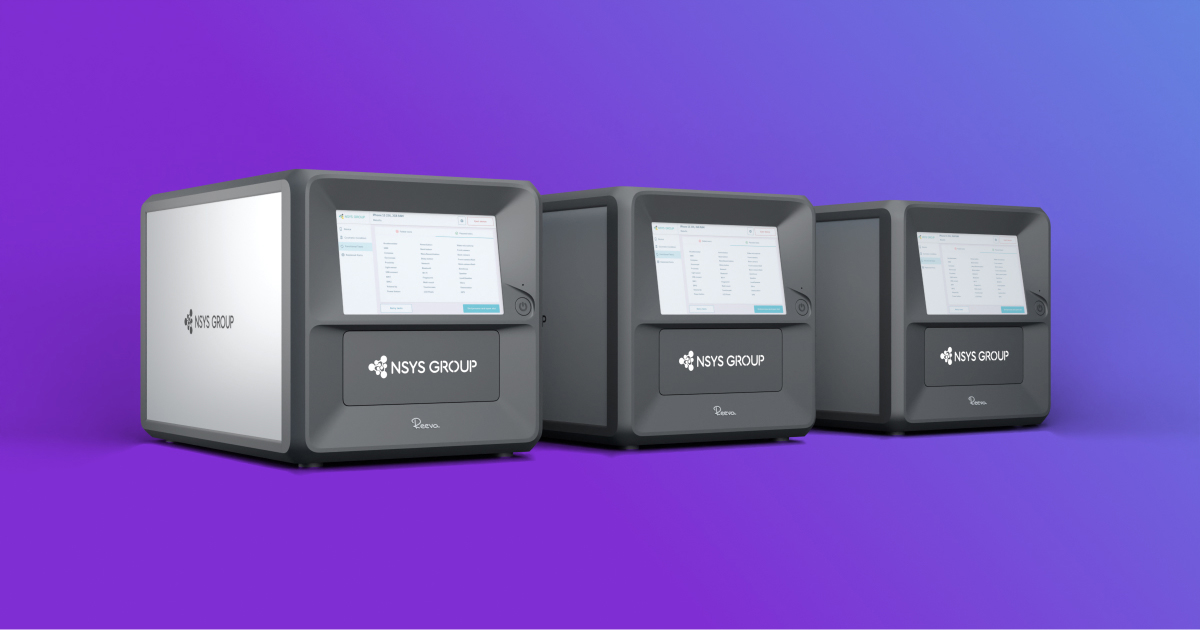
Why Reeva
For Retail stores, machine testing offers a comprehensive, automated evaluation process for buyback.
- Increased Buyback Volume: The automated and straightforward process empowers employees to do buyback confidently. Consumers are attracted to the novelty of a robotic unit.
- Higher Conversion from Inquiry to Buyback: A more accurate evaluation means reduced risks of buying defective techniques, leading to better consumer prices.
- Enhanced Consumer Trust: Independent and automated evaluation process bolsters consumer confidence.
- Reduced Losses and Risks: Certified diagnostics minimizes fraudulent claims, which means protection from Assessment Errors.
- Competitive Edge and Scalability: it offers a unique selling proposition, setting businesses apart.
For Warehouses, Reeva ensures a thorough, automated evaluation process during batch intake.
- Consistent Evaluation Results: Reeva eliminates human errors and subjectivity, ensuring consistency.
- Productivity and Scalability: Robo-lines, consisting of one operator and four robots, enhance productivity, especially when handling large volumes.
- Labor Cost Reduction: Fewer operators are needed for this work, allowing human resources to focus on other tasks.
- Competitive Supplier Advantage: Robotic testing gives suppliers a competitive edge.
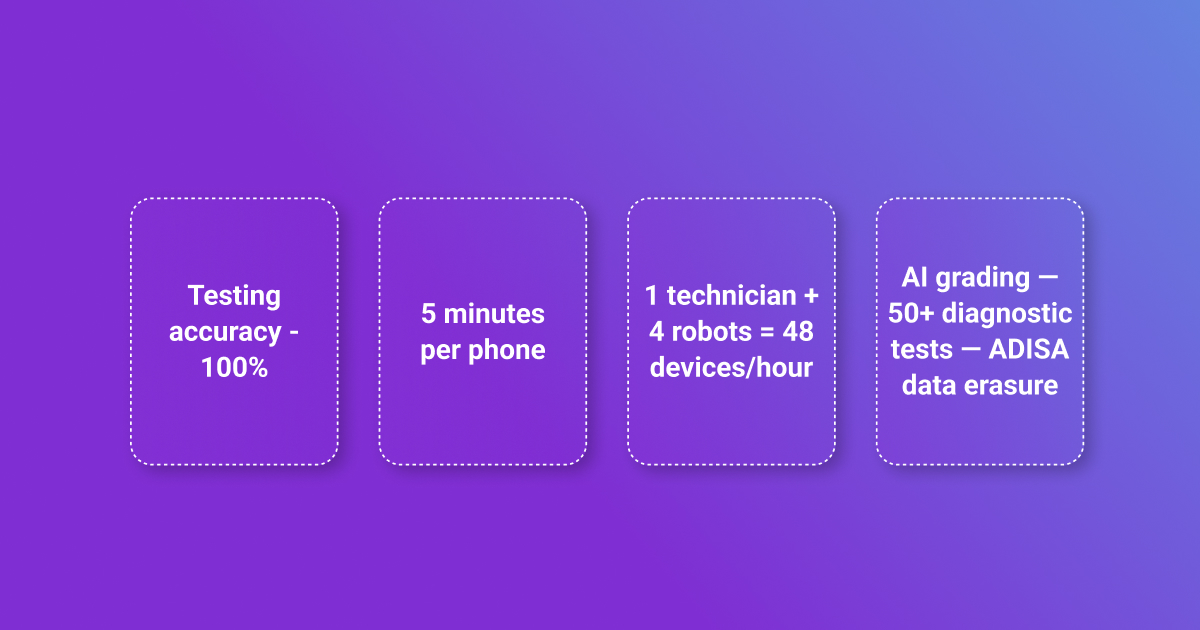
How mobile devices testing with Reeva works
Step 1: The client puts the device in the tray
Step 2: Reeva evaluates it:
- AI Grading customizable for your grading system.
- Diagnostics 50+ tests detect more than 100 defects.
- Data Erasure. Certified by ADISA, compliant with NIST and GDPR. To find out more about data distraction methods and certifications, read our article on the topic.
Step 3: Reeva price the device automatically according to your NSYS Buyback settings
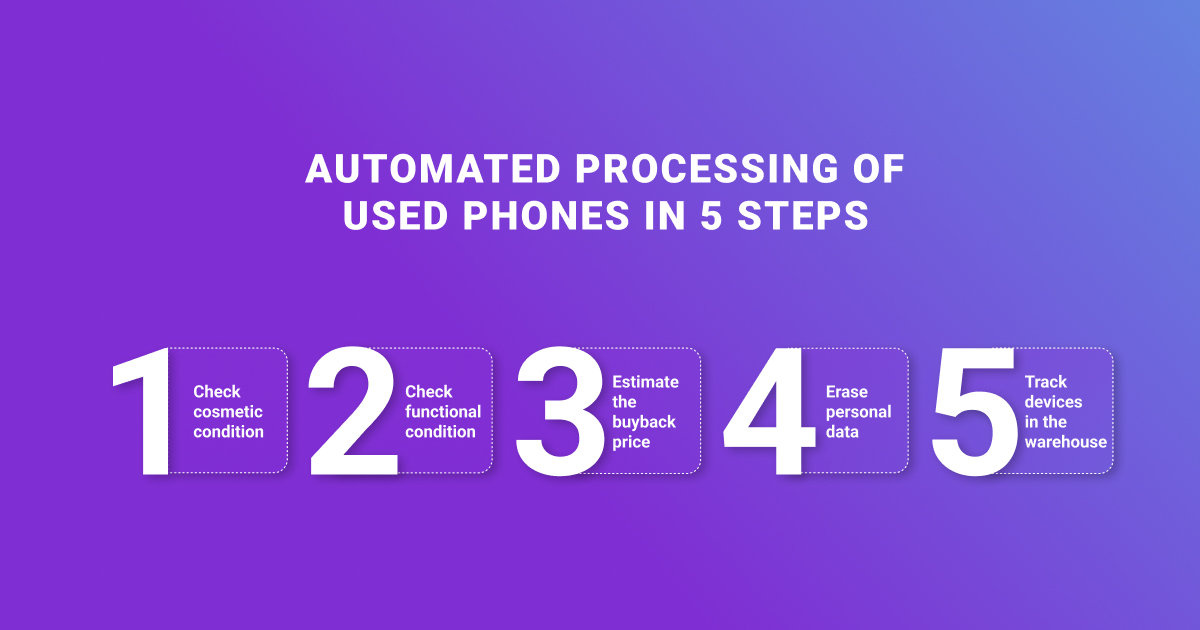
Which mobile device testing tool is your best fit?
We discussed each method's advantages and disadvantages to make diagnostic scenarios more transparent and coherent for you. Choosing a testing method for Android and iOS devices depends on the business's scale and objectives.
Manual diagnostics is practical for small businesses, offering immediate functional checks without extra investment. However, it's prone to human errors.
Large enterprises benefit from software testing, which delivers rapid and precise automated tests, covering a wide range of functions on many operating systems.
Mobile App Testing for Android and Ios
For those prioritizing utmost efficiency and precision and who can allocate a higher budget, robotic testing systems like Reeva from NSYS are ideal, handling multiple devices with impeccable accuracy.
Constantly updating procedures to match market developments and incorporating automated grading ensures standardized results. Ultimately, the choice of testing process should align with the business's specific needs, aiming for consistent quality to ensure both customer satisfaction and profitability.
If you want to experience the power of software and robotic technologies, leave a request, and we will calculate the benefits of NSYS automation for your case!